Head of the laboratory: Prof. dr Milija Kraišnik
Contact: 057/340-847, ext. 106
E-mail: milija.kraisnik@ues.rs.ba
Laboratory for welding and testing of materials
Laboratory equipment and activities:
Welding section
1. Industrial AC/AD machine for TIG and REL welding process – type MagicWave Comfort 3000 – 2 working places
Digitally controlled TIG-AC / DC power supply
Mobile use in the chemical, process and machine industries
Welding of high and low alloy steels, aluminum and its alloys, as well as non-ferrous metals
It is intended for the realization of TIG-DC, TIG-AC/DC and REL welding procedures
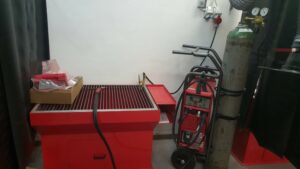
2. Industrial machine for MIG and MAG welding process – type TransPuls 3200 Synergic – 2 working places
Fully digitized and microprocessor-controlled MIG / MAG power supply with 320 A current
Welding in the aerospace, automotive, chemical, process, machine industry, etc
Welded components: aluminum, Cr-Ni steel, construction steel and special metals
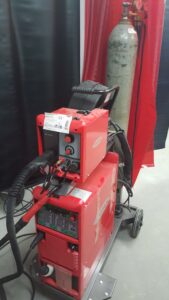
3. Portable MMA and TIG welding machine – type TransPocket 1500 TIG – 1 working place
Guaranteed stability of work and selected welding parameters
Welding of construction steels, stainless steels, aluminum, cast iron, special materials
Scope / procedures:
TIG-DC welding with microprocessor control of arc contact ignition and special end current function – TIG Comfort Stop / TCS / with regulation of welding current on the TIG burner itself.
TIG-DC pulsed current welding with microprocessor control of arc contact ignition and special end current function – TIG Comfort Stop / TCS / with regulation of the welding current on the TIG burner itself.
REL welding with all types of coated electrodes up to ∅ 4.0 mm
REL welding with cellulose electrodes, vertically downwards, up to ∅ 4.0 mm
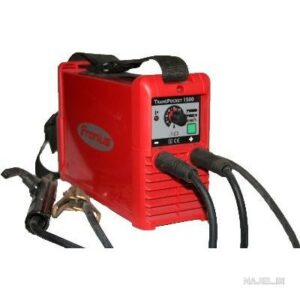
4. Plasma cutting device – type PowerMax 45 – 1 working place
The most common portable plasma cutting machine on the market with a wide range of possibilities.
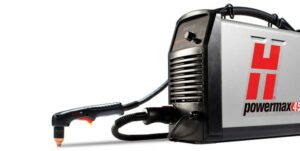
5. Gas welding and cutting equipment – 1 working place
Oxygen and acetylene bottles
Gas burner and cutting torch set
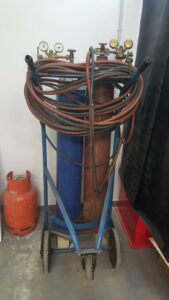
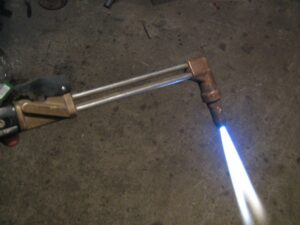
Potentially possible activities of the welding section
Based on the available devices, equipment, additional materials and accessories, Laboratory for welding and testing of materials: Welding section, the following activities can be realized:
Educational aspect
- Introducing students to modern equipment and devices for welding MAG, MIG, TIG, REL and gas welding process, as well as gas and plasma cutting procedures;
- Practical demonstration of MAG, MIG, TIG, REL and gas welding procedures and gas and plasma cutting procedures;
- Introducing students to additional materials used for the implementation of the above welding procedures;
- Realization of various laboratory exercises in the studies of the first and second cycle, which are based on the above welding and cutting procedures for the purpose of preparing seminar papers, project assignments, final and master papers;
- Organizing a summer welding school for students from other universities for the purpose of presenting the capacity of the Faculty of Mechanical Engineering, University of East Sarajevo and popularizing the machine profession;
- Organization of lectures by eminent experts in the field of welding and related joining techniques.
Scientific and professional aspect
- Realization of experimental research based on the mentioned welding and cutting procedures for the purpose of publishing scientific-professional papers and preparation of master’s theses and doctoral dissertations;
- Scientific research activities within the implementation of national and international projects;
- Cooperation with other related laboratories from the surroundings in order to exchange knowledge and experience in the field of welding, cutting and control of welded joints.
Commercial aspect
- Preparation of project documentation for MAG, MIG, TIG, REL and gas welding process, as well as gas and plasma cutting process;
- Organization of seminars for the purpose of additional theoretical and practical education and training of welders in the context of lifelong learning;
- In cooperation with economic entities, organization of additional training with a special focus on certain welding procedures;
- Organization of training for the purpose of retraining workers;
- Welding and cutting services by the aforesaid operations in accordance with the technical capabilities of devices and equipment.
Consulting in the field of welding conventional materials.
Materials testing section
1. Test machine SHIMADZU AGS-X 20 kN
Measuring cell with nominal load 20kN
Extensometer – basic measuring length 25 mm
Implements tests of tension, compression, bending in three points and determination of the coefficient of static and kinematic friction
Self-calibration, shock detection / self-recovery
Effective width: min. 420 mm or better
Distance between frame and base: min. 1200 mm or better
Instrument compliant with EN 10002-2, ISO 7500-1, and ASTM E4 standards
Measuring cell with a load of 20kN, with all the necessary accessories for smooth operation with mechanical jaws and packs for receiving material 3 sets (packs from 0 to 7 mm, from Ø4 to Ø9 mm, from Ø9 to Ø14 mm)
Additive for testing materials for pressure and bending
Compression plate, for pressure testing (Ø100 mm)
Additional tool for testing the bending of the material in three points
Extensometer with basic length 25 mm, elongation during measurement 10% (2.5 mm)
Reception of flat samples up to 10 mm thick, bar up to 14 mm with all the necessary parts for installation and smooth operation
Friction test tool (up to 10kN)
Appropriate software (test methods that comply with all standards including pressure, tension, bending, adhesion and shear, calculation and processing of data obtained by testing on the instrument, creating reports, the possibility of program protection)
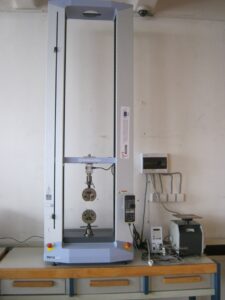
2. Abrasive cutting machine METACUT 302
Machine power – 3 kW
Speed – 2800 rpm
Cutting plate diameter – Ø300 / Ø250 mm
Cutting capacity – Ø115 / Ø90 mm
Cutting capacity – 50 x 195/50 x 165 mm
Dimensions of the table with T-slot – 255 x 250 mm
T-slot dimensions – 12 mm
Size, WxLxH – 58 x 68 x 49 cm
Mass – 132 kg
Colling unit – 60 l
Power supply – 3 phases 400 V, 50 Hz
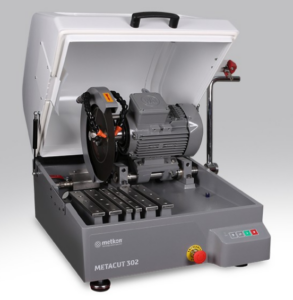
3. Grinding and polishing machine FORCIPOL 102
Number of disks – 1
Disc diameter – Ø250 mm
Machine power – 1 kW
Speed – 50-600 rpm
Roller rotation direction – left / right
Dimensions WxLxH – 45 x 74 x 34 cm
Mass – 50 kg
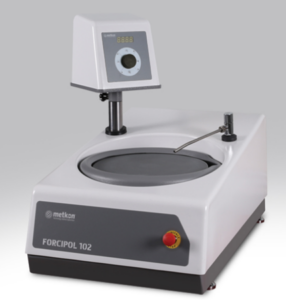
4. Metallographic microscope BS-6010
Eyepieces – WF 10x / 20 and EW 20x / 12
Lenses – 5x / 0.12 BF / DF LWD 10mm
10x / 0.25 BF / DF LWD 10mm
20x / 0.40 BF / DF LWD 5mm
50x / 0.75 BF / DF LWD 1.3mm
100x / 0.90 BF / DF LWD 0.7mm
Triocular metallographic microscope with Infinite optical system
Siedentopf trinocular head, 30°, interpupillary distance 48-75mm
Two-layer object table 216x150mm, displacement range 78x54mm
Coaxial rough and fine adjustment, fine division 2µ, displacement range 30 mm
5. Digital microscope color video camera DIGI 1000
Sensor – CMOS 10 MP
Progressive scan
Maximum resolution – 3664 × 2748
Pixel size – 4.65 x 4.65 μm
Dynamic range – 70dB
Exposure – normally 0.22 – 119.37ms
6. Licensed MetaPlus software Dewinter
Quantitative image analysis system with modules specific to the steel industry. Industry standards EN ISO 643, ASTM E-12, ASTM E-930-92 and ASTM 13 82-91.
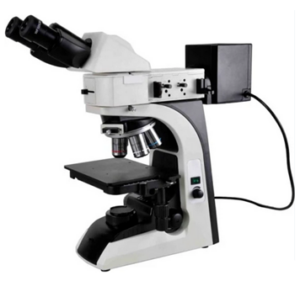
Potentially possible activities of the materials testing section
Based on the available devices and equipment in the Laboratory for welding and testing of materials: Materials testing section, the following activities can be realized:
Educational aspect
- Introducing students to modern equipment and devices for macroscopic and microscopic examination of materials;
- Providing practical classes in subjects related to material structure testing and testing of welded joints;
- Introducing students to the process of metallographic preparation of test specimens, which includes cutting on an abrasive cutting machine, casting, grinding and polishing, as well as preparation of samples in a caustic agent;
- Work on metallographic microscope with magnification up to 2000x, as well as on optical microscopes of lower magnification;
- Realization of various laboratory exercises in the studies of the first and second cycle for the purpose of making seminar papers, project assignments, final and master papers.
Scientific and professional aspect
- Realization of experimental research for the purpose of publishing scientific-professional papers and preparation of master’s theses and doctoral dissertations;
- Scientific research activities within the implementation of national and international projects;
- Cooperation with other related laboratories from the surroundings in order to exchange knowledge and experience in the field of macroscopic and microscopic testing of materials and welded joints.
Commercial aspect
University of East Sarajevo, Faculty of mechanical engineering East Sarajevo, Center of accredited laboratories has accredited 7 methods of testing metals and welded joints:
No. | Materials / products | Type of test/Measurement characteristic | Measuring range | Methods / Specifications |
1. | Metals and metal products | Tensile testing – Part 1: Room temperature test | (2 – 20) kN | BAS EN ISO 6892-1:2021 |
2. | Metals and metal products | Bending test | (2 – 20) kN | BAS EN ISO 7438:2017 |
3. | Metals and metal products Welded metal materials |
Destructive testing of welded joints on metal materials – Tensile testing of transverse specimens |
(2 – 20) kN | BAS EN ISO 4136:2014 |
4. | Metals and metal products Welded metal materials |
Destructive testing of welded joints on metal materials – Bending test |
(2 – 20) kN | BAS EN ISO 5173:2011 |
5. | Metals and metal products Welded metal materials |
Destructive testing of welded joints on metal materials – Microscopic testing |
2000X | BAS EN ISO 17639:2014 |
6. | Metals and metal products | Microscopic determination of apparent grain size | 2000X | BAS EN ISO 643:2014 |
7. | Metals and metal products Welded metal materials |
Destructive testing of welded joints on metal materials – Macroscopic testing |
50X | BAS EN ISO 17639:2014 |